Enhancing Efficiency with Case Erector Bottom Sealers
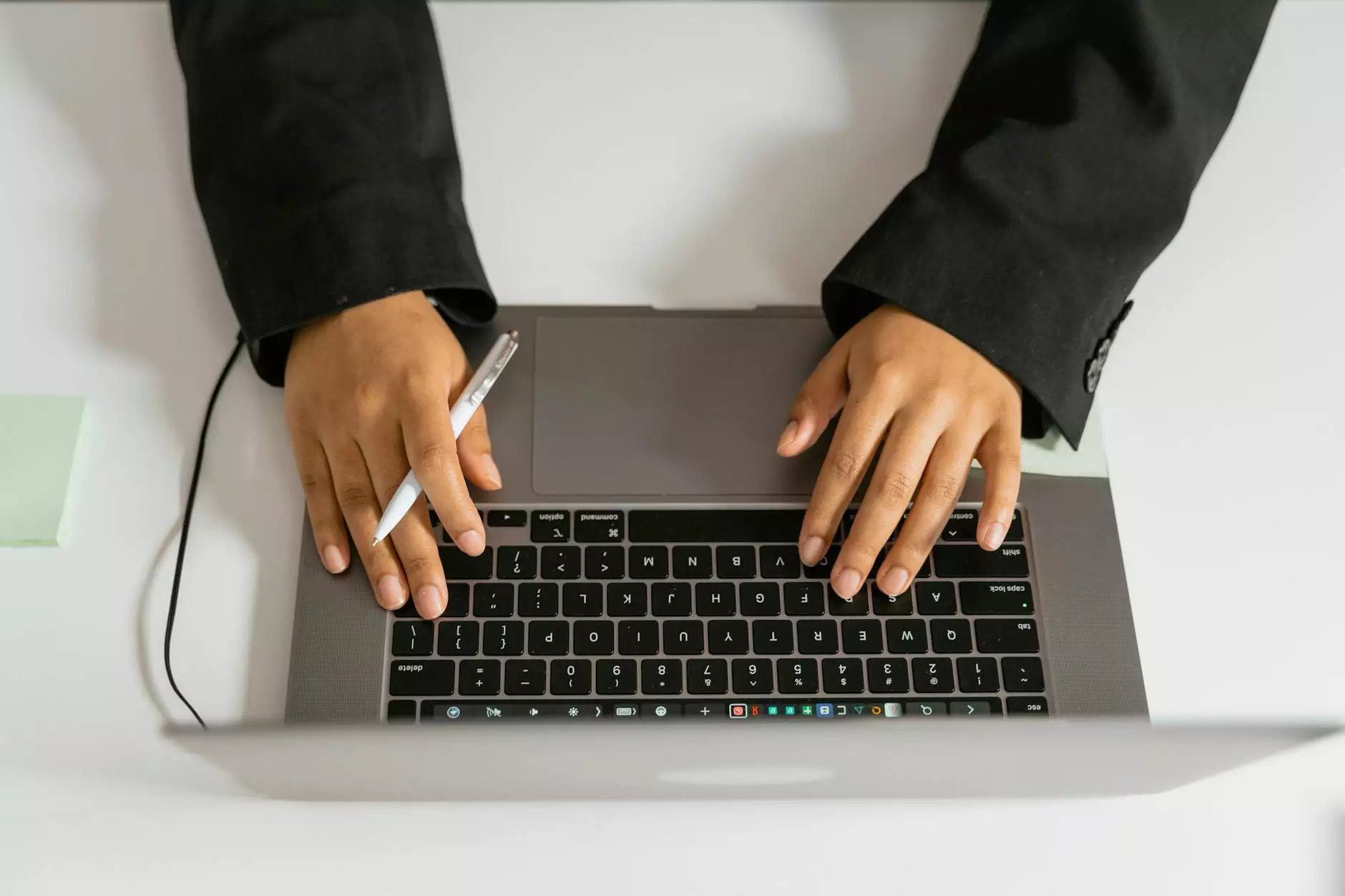
In the dynamic world of packaging equipment manufacturing, finding innovative solutions that enhance productivity and streamline operations is crucial. Case erector bottom sealers emerge as an essential tool for businesses striving to optimize their packaging processes. They play a pivotal role in ensuring that products are securely packaged, promoting efficiency, and ultimately contributing to better output in manufacturing environments.
Understanding Case Erector Bottom Sealers
A case erector bottom sealer is a specialized machine designed to fold and seal the bottom of cardboard boxes or cases. The versatility and efficiency of these machines make them invaluable in various industries, including food and beverage, pharmaceuticals, consumer goods, and electronics. By automating the packaging process, businesses can reduce manual labor costs, minimize errors, and increase production rates.
The Core Functions of Case Erector Bottom Sealers
- Box Formation: The machine quickly forms boxes from flat sheets of cardboard, ensuring uniformity and structural integrity.
- Bottom Sealing: Once the boxes are formed, the bottom flaps are sealed using adhesive or tape, securing the contents for transport.
- Integration with Other Equipment: These machines can be seamlessly integrated into existing packaging lines, working in conjunction with fillers and labelers.
Benefits of Using Case Erector Bottom Sealers
The adoption of case erector bottom sealers offers a host of advantages that can significantly impact a business's bottom line. Here are some key benefits:
1. Increased Production Efficiency
By automating the case forming and sealing process, companies can achieve higher output rates. Traditional manual methods often lead to bottlenecks and delays; however, with a case erector bottom sealer, boxes can be created and sealed in a matter of seconds, enabling smoother operations and faster product delivery.
2. Cost Savings
Investing in automated packaging solutions like case erector bottom sealers leads to significant cost savings. Reduced labor costs, decreased material waste, and lower risk of damage during packaging can greatly enhance profitability. Furthermore, their efficiency reduces the time spent on packing lines, allowing businesses to allocate resources more effectively.
3. Improved Packaging Quality
The precision engineering of case erector bottom sealers ensures that boxes are formed and sealed consistently and securely. This not only enhances the aesthetic appeal of the packaging but also protects the product from damage during shipping and handling. Better packaging quality translates to fewer returns and higher customer satisfaction.
4. Enhanced Safety
Automation of the packing process substantially reduces the risk of workplace injuries associated with manual handling. With a case erector bottom sealer in place, employees can focus on other essential tasks while minimizing exposure to hazardous activities, thereby fostering a safer work environment.
5. Flexibility and Customization
Many modern case erector bottom sealers come with adjustable settings to accommodate varying box sizes and styles. This versatility allows manufacturers to adapt to changing market demands quickly, ensuring they can meet diverse customer requirements without investing in multiple machines.
Key Features to Look for in Case Erector Bottom Sealers
When selecting a case erector bottom sealer, various features are critical for ensuring optimal performance and integration into existing packaging systems:
- Speed: Look for machines capable of handling high volumes, ideally with adjustable speeds to match production needs.
- Durability: Choose equipment made from high-quality materials that can withstand the rigors of daily use.
- Easy Maintenance: Opt for models with straightforward maintenance and service procedures, minimizing downtime.
- Modular Design: Pick a sealer that can be easily integrated with existing machinery and accommodate future upgrades.
- User-Friendly Controls: Ensure the machine has intuitive interfaces and controls, making it accessible to various operators.
The Technology Behind Case Erector Bottom Sealers
The technology that drives case erector bottom sealers has evolved considerably, incorporating advanced automation and control systems. Here are some technological innovations to consider:
1. Robotics
Some modern machines utilize robotic arms for precise handling of box materials. Robotics can enhance speed and flexibility, allowing for greater adaptation to different box styles and sizes.
2. Sensors and Automation
Advanced sensors can monitor the entire packaging process, ensuring accurate box dimensions and sealing performance. Automation helps in error detection and correction, reducing the likelihood of downtime caused by manual inspection.
3. Smart Technology and IoT Integration
With the rise of the Internet of Things (IoT), many newer models can connect to the cloud, allowing for real-time monitoring and data analysis. This connectivity provides manufacturers with insights to optimize operations and preemptively address issues before they escalate into costly problems.
How to Integrate Case Erector Bottom Sealers in Your Packaging Line
Integrating a case erector bottom sealer into your existing packaging line requires careful planning and execution. Here's a step-by-step guide to facilitate a smooth integration:
1. Assess Current Operations
Evaluate your current packaging processes. Identify bottlenecks and areas where speed and quality could improve. Understanding your operational workflow is fundamental to determine where the new equipment will fit.
2. Determine the Right Model
Based on your assessment, research different models that meet your production demands. Consider factors such as speed, flexibility, and maintenance requirements. Engaging with a reputable equipment manufacturer like shineben.com can provide tailored recommendations.
3. Plan Layout and Space Requirements
Analyze the physical space in your facility to determine how to integrate the new case erector bottom sealer. Ensuring proper space allocation will enhance operational flow and efficiency, reducing the chances of congestion on the production floor.
4. Training and Transition
Ensure that your staff is well-trained in operating the new equipment. Comprehensive training can significantly ease the transition, promoting confidence among operators and minimizing the learning curve.
5. Monitor and Optimize
Once the case erector bottom sealer is integrated, continuously monitor its performance. Collect data on production rates, seal quality, and operational efficiency. Use this data to make informed decisions on further optimization of your packaging processes.
Conclusion
In today's fast-paced business environment, leveraging the right technology can be the difference between success and stagnation. Case erector bottom sealers represent a significant advancement in the packaging industry, enabling businesses to enhance their efficiency, cut costs, and improve product quality. As companies adapt to evolving market demands, investing in automated packaging solutions such as these will remain an essential strategy for achieving operational excellence.
For businesses looking to streamline their packaging operations and elevate their production capabilities, resources available at shineben.com provide comprehensive information and solutions tailored to your specific needs. Consider joining the growing number of manufacturers that enjoy the benefits of case erector bottom sealers, ensuring scalability, flexibility, and sustained growth in an ever-competitive landscape.