Elevating Manufacturing with CNC Mold Makers
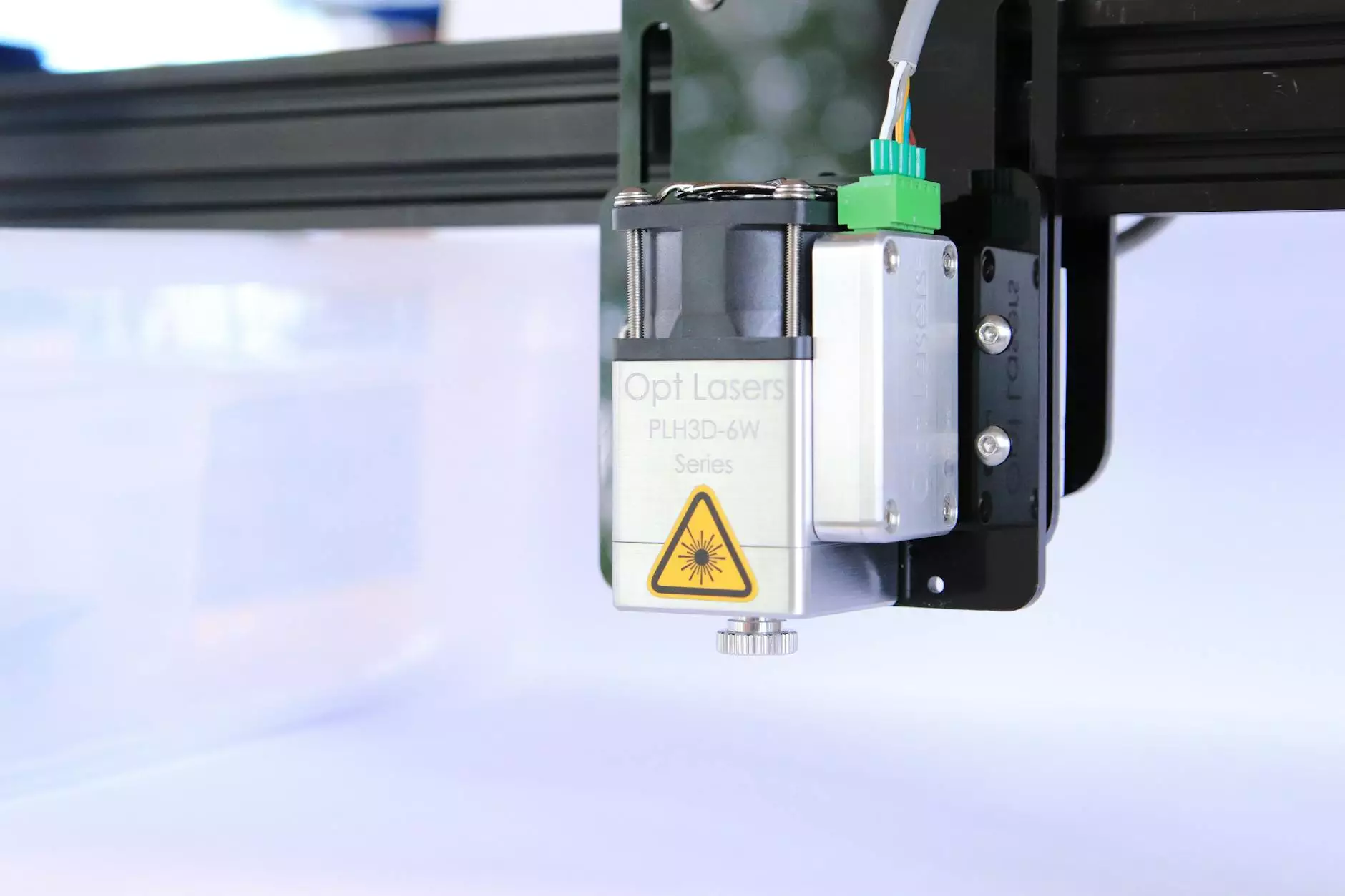
In the ever-evolving landscape of manufacturing, cnc mold makers play a pivotal role in driving innovation and enhancing production efficiency. These specialists not only create molds but also ensure that the manufacturing process is streamlined, precise, and adaptable. This article delves deep into the vital contributions of CNC mold makers, exploring their techniques, advantages, and the impact they have on various industries.
The Role of CNC in Modern Manufacturing
CNC, or Computer Numerical Control, refers to the automation of machine tools using computers. This technology revolutionizes traditional fabrication methods. The integration of CNC technology into mold making is a game changer that provides unmatched precision and consistency in the production process.
Precision Engineering
At the heart of CNC mold making lies precision engineering. CNC machines operate using a set of coded instructions, allowing for micro-level accuracy in every cut and fabrication. This is crucial when producing molds that require exact specifications, as even the slightest deviation can lead to defective products.
- Advanced Design Capabilities: Using CAD (Computer-Aided Design) software, CNC mold makers can create intricate designs that meet specific production requirements.
- Efficient Prototyping: With CNC technology, prototypes can be developed quickly and with high fidelity, significantly speeding up the design process.
- Customization: CNC machines allow for easy modifications, enabling manufacturers to adapt to changing market demands swiftly.
Key Benefits of Employing a CNC Mold Maker
Utilizing a cnc mold maker can offer several advantages that can enhance the overall production process:
1. Enhanced Efficiency
CNC machines operate continuously without fatigue, leading to higher production rates. This efficiency means businesses can meet customer demand without sacrificing quality.
Moreover, the consistency of CNC output minimizes waste and reduces the time required for finishing processes, which is vital for meeting tight deadlines.
2. Quality Assurance
Quality control is a critical aspect of manufacturing, and CNC mold makers excel in this area. The advanced software used in CNC machining monitors every aspect of the production process, ensuring that the final product meets the required standards consistently.
3. Cost-Effectiveness
While the initial investment in CNC technology can be significant, the long-term savings can be substantial. The reduction in material waste, labor costs, and rework all contribute to a lower overall expenditure.
Additionally, CNC mold makers' ability to produce high-quality molds reduces the risks associated with defective products, leading to increased customer satisfaction and loyalty.
Industries That Benefit from CNC Mold Makers
The versatility of CNC mold making means it finds applications across various industries. Here are some sectors that greatly benefit:
- Aerospace: Precision is paramount in aerospace manufacturing, where every component must adhere to strict regulations and safety standards.
- Automotive: The automotive industry relies heavily on CNC molds to produce parts that are both reliable and efficient.
- Consumer Products: From electronics to appliances, CNC mold makers create components that meet customer needs for functionality and aesthetics.
- Medical Devices: Precise molds are crucial in the medical field, ensuring that devices function as intended and meet rigorous safety criteria.
The Process of CNC Mold Making
Understanding how CNC mold making functions can provide deeper insights into its benefits and applications.
Step 1: Design Phase
The journey begins with a comprehensive design phase. Engineers and designers utilize advanced CAD software to create a detailed mold design that considers functionality, aesthetics, and manufacturability.
Step 2: Selecting the Material
The choice of material is critical, as it directly affects the mold's durability and the quality of the final product. Common materials include:
- Steel: Offers high durability and strength, ideal for mass production.
- Aluminum: Lightweight and cost-effective, suitable for prototypes and low-volume production.
- Plastics: Used for molds that require flexibility and lower production costs.
Step 3: Machining the Mold
Once the design is finalized and materials chosen, the CNC machines take over. These machines execute the programmed instructions, cutting, shaping, and finishing the mold with unparalleled accuracy.
Step 4: Quality Inspection
After machining, each mold undergoes rigorous quality checks. This ensures that it meets all specifications before it goes into production, which is crucial for maintaining standards.
Innovations in CNC Mold Making
The field of CNC mold making is continually evolving. Innovations drive improvements in efficiency, quality, and capabilities.
Automation and Smart Technologies
Integrating smart technology and automation into CNC machining processes enables real-time monitoring and adjustments. This leads to adaptive machining, where molds can be adjusted on-the-fly to improve outcomes.
Advanced Materials
Developments in new high-performance materials enhance the capabilities of CNC molds, allowing for more complex and durable products. These materials improve thermal stability and resistance to wear, making them ideal for demanding applications.
Choosing the Right CNC Mold Maker
Selecting a reliable cnc mold maker is crucial for successful collaboration and optimal results. Here are factors to consider:
- Experience and Expertise: Ensure that the mold maker has extensive experience in the specific industry relevant to your needs.
- Technology and Equipment: Check that they utilize the latest CNC technology and maintain their equipment to high standards.
- Portfolios and References: Review their past projects and obtain references to assess their quality of work and customer satisfaction.
- Flexibility: A good mold maker should be willing to adapt to your project requirements and timeline.
Conclusion: The Future of CNC Mold Making
As we look to the future, the role of cnc mold makers will only become more critical in the manufacturing sector. Their ability to produce high-quality, precision molds efficiently positions them as invaluable partners in various industries.
With advancements in technology and materials, CNC mold making will continue to innovate, leading to even greater levels of customization and efficiency. Businesses seeking to thrive in the competitive market must recognize the importance of aligning with skilled CNC mold makers who can support their vision and operational needs.
By choosing to invest in quality CNC mold making solutions, manufacturers can expect enhanced productivity, reduced costs, and improved product quality. This strategic move will not only foster growth and innovation within their companies but also secure a competitive advantage in an increasingly global marketplace.
Visit deepmould.net to learn more about how our services can elevate your production capabilities with our expert cnc mold maker solutions.